CNC-Fräse/Portal Fräse Eigenbau
(Computerized Numerical Control)
Ursprünglich wollte ich mir einen Frästisch für eine Oberfräse bauen, da ich eine Reihe von Teile herstellen möchte/muss, die aufgrund der Genauigkeit nur gefräst werden können. Dennoch gab es einige Dinge, die mich an einer Oberfräse gestört haben.
Zum einen bleibt auch bei einem Frästisch letztendlich das Problem, dass man sämtliche Einstellungen manuell vornehmen muss. Vor allem möchte ich aber vorwiegend Aluminium- und Carbon-Teile herstellen. Also habe ich mir gedacht, warum nicht gleich eine elektronische Fräse bauen. Da natürlich auch in diesem Umfeld keine Grenzen gesetzt sind, sollte es für den Anfang erst einmal eine Fräse mit überschaubaren Kosten sein. Upgraden kann man immer noch!
Wer im Internet ein wenig zum Thema "Eigenbau CNC-Fräse" recherchiert stößt unweigerlich auf die MPCNC. Bei dieser CNC-Fräse handelt es sich um eine CNC-Fräse aus dem Hobby-Bereich, die größtenteils per 3D-Druck erstellt werden kann. Entweder kauft man sich die Teile oder druckt sie selbst auf dem eigenen Drucker aus. Der Download ist kostenlos per Thingiverse oder über die V1Engineering-Homepage verfügbar.
Ehrlich gesagt stelle ich hier schon meine 2. CNC-Fräse vor. Bei der 1. CNC-Fräse (MPCNC Burly) habe ich die Teile noch direkt gekauft, da meine Kenntnisse im 3D-Druck noch nicht so fortgeschritten waren. Vor allem muss man jedoch auch betonen, dass der Ausdruck der Teile gut und gerne ca. 180 - 200 Stunden (insgesamt) dauert und das auch nur, wenn keine Probleme auftreten und man ggf. nicht mehrfach einen Druck anstarten muss. Kauf oder Selbstdruck sollte daher gut überlegt werden.
Hier mal ein Zwischenstand, wie die CNC-Fräse ungefähr mal aussehen sollte.

Da die 1. CNC-Fräse (MPCNC BURLY) schon wieder "Geschichte" ist, dann doch direkt der Bau der 2. Fräse, die MPCNC PRIMO. Bei dieser Fräse habe ich mich dazu entschieden, die Teile selbst auszudrucken, aus folgenden Gründen:
- Bei dem Material der Kaufvariante handelt es sich um PLA mit 35 - 40% Infill, ich wollte der höheren Festigkeit halber überwiegend andere Materialien einsetzen wie: PTE, CPE HG100, ASA
- Da ich noch verschiedene Filamente übrig hatte, wollte ich einige Drucktests machen, zu denen sich die Teile der MPCNC Primo bestens eigneten
- Falls PLA zum Einsatz kommt, dann jedoch mit einem höheren Infill - in der Größenordnung 60 - 70%
- Es war von vornherein klar, dass die Standard-Variante der MPCNC PRIMO nicht aufgebaut werden sollte. Daher wurden eine Reihe von Teilen gar nicht erst benötigt, mussten daher auch nicht mit dem 3D-Drucker gedruckt werden.
- Vielmehr habe ich direkt eigene Teile kreiert und gedruckt.
- Hauptgründe für die Modifikationen und eigenen Teile waren von vornherein eine höhere Festigkeit/Stabilität der Fräse sowie höhere Präzision.
Aus den oben genannten Gründen ist die Fräse dann auch recht bunt geworden, frei nach dem Motto:
COLOUR YOUR WORLD!
Auch wenn die Farbpracht vielleicht etwas verwirrt, die Gesamt-Stabilität und Präzision der Fräse sollte durch die Materialien um ein vielfaches höher werden als die normale Standard-Variante.

Hier mal einige der Standard-Komponenten. Es sei dazu gesagt, im oberen Bereich des Fotos finden sich schon Komponenten aus CARBON PC, die bereits für ein anderes Projekt gedacht sind, dem Umbau des Prusa i3 MK3S zu einem Hochtemperatur 3D-Drucker.
CARBON PC wollte ich für die MPCNC PRIMO nicht unbedingt nutzen, aber vielleicht kommt es noch. Der Materialpreis für CARBON PC ist in einer Größenordnung, wo man dann doch überlegen sollte, sich eine andere CNC-Fräse aus Metall zu bauen und nicht zu drucken.
Hier mal im Folgenden etwas zu den Materialien.

Teile (Foto oben)
- Ecken (Standard), in denen die Führungsrohre montiert werden. Die Ecken bestehen immer aus 2 Teilen (oben/unten) und wurden 2-farbig ausgedruckt. Dann ist es einfacher, sie zusammenzuführen.
- Füße (Eigenentwicklung, unteres Foto am oberen Rand), die auf den 30x30 Aluminium-Profilen aufgesetzt werden und die Profile mit den Ecken verbinden.
Material/Druckeigenschaften
- Material: PLA
- Farben: blau und schwarz
- Layer height: 0.3 mm
- First layer: 0.2 mm
- Infill: 70%
- Extrusion width: 0.75 mm / No rafts, no support
- Temperature: 215°C / 60°C
- Cooling: min. 100% / max. 100%
PLA ist natürlich das Standard-Filament und recht einfach zu handhaben. Aus meiner Sicht gibt es jedoch interessantere Alternativen, vor allem wenn es um höhere Beständigkeiten geht. Hier vor allem: Temperatur, Flüssigkeiten etc.
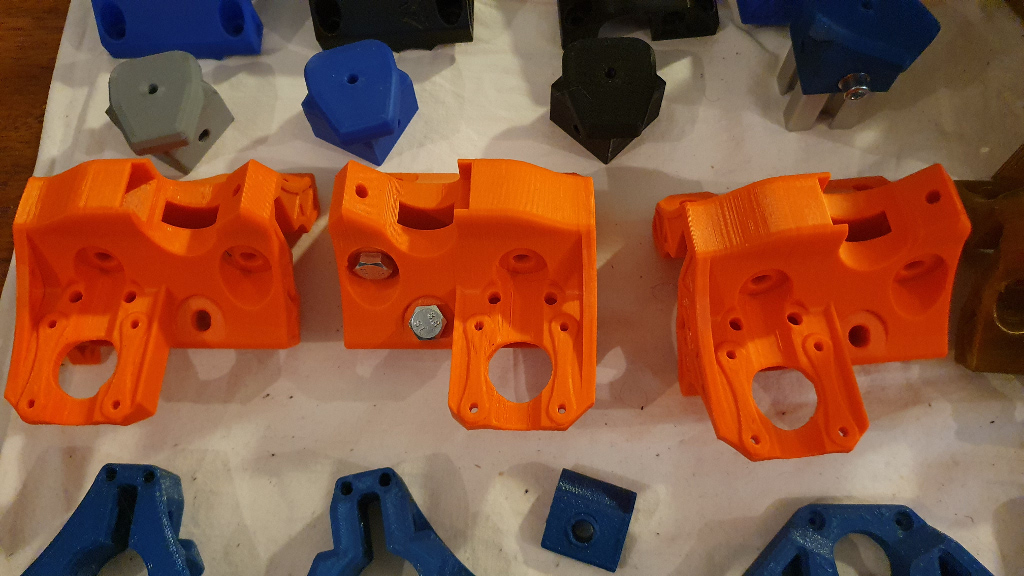
Teile (Foto oben)
- Trucks, für Stepper-Motoren und Führungsschienen (orange)
Material/Druckeigenschaften
- Material: ASA
- Farben: orange
- Layer height: 0.3 mm
- First layer: 0.2 mm
- Infill: 50%
- Extrusion width: 0.75 mm
- Skirt height: 30 Layer min. (falls der Drucker nicht in einem Gehäuse steht. Ansonsten gibt es massive Probleme mit Warping, bis hin zum Crash, da das Teil sich bei der langen Druckdauer lösen wird!), Loops: 3 - no supports
- Temperature: 260C / 110°C
- Cooling: off, no cooling!!! (WICHTIG!)
Ehrlich gesagt wird ASA nicht zu meinen bevorzugten Materialien gehören. Die Stabilität ist natürlich um einiges besser als bei PLA oder PETG und auch die Temperaturbeständigkeit ist wesentlich höher. Auf der anderen Seite sind die notwendigen Arbeitstemperaturen von Düse (>250°C) und Druckbett (>100°C) charakteristisch. Hinzu kommt der Geruch, der ohne Lüftung des Raumes (siehe Luftzug und Warping) doch irgendwann Kopfschmerzen verursacht. Größtes Problem ist jedoch die hohe Tendenz des Warping, wenn man kein Druckergehäuse besitzt. Man muss zumindest einen "Schutz" mitdrucken, ansonsten lösen sich die Teile bei längeren Druckzeiten bzw. verziehen sich sichtbar. Zudem weisen die Teile recht hohe Materialspannungen auf, empfehlenswert ist daher ein nachträgliches Tempern der Teile. Für die Trucks jedoch eine gute Materialwahl, auch wenn ich zukünftig ASA durch andere Materialien ersetzen werde.

Teile (Foto oben/unten)
- Truck, für Stepper-Motoren und Führungsschienen
- Core für Z-Achse
- Schlussendlich noch Clamps für den Core - in dem die Lager der Core-Führung eingebaut werden
Material/Druckeigenschaften
- Material: CPE HG100
- Farbe: Morning Sun - bei der Farbe geht jedesmal die Sonne auf
- Layer height: 0.3 mm
- First layer: 0.2 mm
- Infill: 50%
- Extrusion width: 0.7 mm (!) / No rafts, no support
- Temperature: 270°C / 70°C
- Cooling: min. 20% / max. 25%

CPE HG100 ist wirklich ein tolles Material. Hat man einmal die richtigen Einstellungen im Slic3r gefunden, ist es recht einfach zu handhaben und die Qualität der Ausdrucke ist wirklich Top. Vor allem ist aber die Stabilität, Temperaturresistenz und auch die Widerstandsfähigkeit um einiges höher als PLA ... und der Preis ist auch recht attraktiv!
Aus meiner Sicht eines der empfehlenswerten Materialien. Für Core, Trucks, Clamps und alle Teile, die entsprechenden Kräften ausgesetzt sind, eine gute Wahl
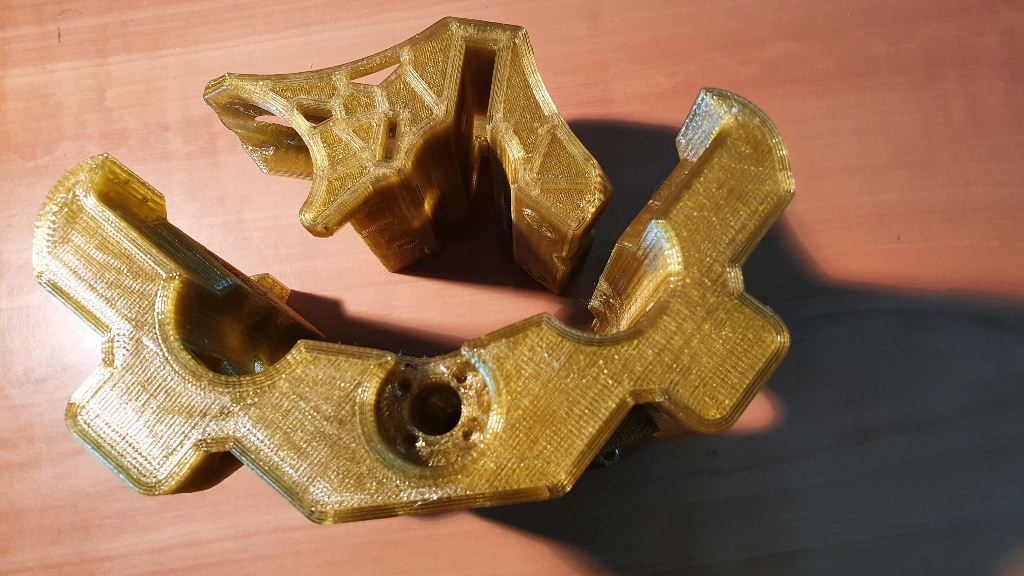
Teile (Foto unten)
- Core Clamps XYZ
- Streben der Z-Achse (Motor und Lager)
- Halterungen für die Zahnriemen
- Stopper für Trucks
- Truck Clamps (für Führungsrohre)
Material/Druckeigenschaften
- Material: PETG
- Farbe: Blue Metallic
- Layer height: 0.3 mm
- First layer: 0.2 mm
- Infill: 50%
- Extrusion width: 0.5 mm (!) / No rafts, no support
- Temperature: 240°C / 90°C
- Cooling: min. 30% / max. 50%

Auch PETG ist ein interessantes Material als Alternative zu PLA. Materialeigenschaften sind in vielen Dingen besser als PLA, Verarbeitung ist relativ einfach und auch der Preis nur geringfügig höher als PLA. Wie gesagt, gute Alternative.